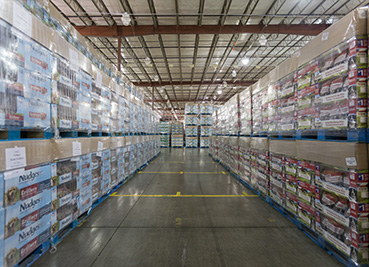
During the past 12 to 14 years, millions of words have been written about “big data” and how to manage it. The fact of the matter is that big data is simply a new term for an old condition. Almost from the first day that technology became widely used in managing the supply chain, we have had more data that we can use. Rather than spending time and resources trying to manage what we don’t need, I believe we should spend our time reducing the amount of data managed to that which we can really use effectively. This could be particularly important in managing the performance of logistics service providers – distribution centers, carriers, and other supply chain partners. In too many cases, outsourcers have become so enamored with data that they measure more than they need to.
In 1610, Galileo Galilei said, “We must measure what can be measured and make measurable what cannot be measured.” (Over the years, this statement has evolved into the more direct, off-quoted axiom,” You cannot manage what you cannot measure. “). But today, more than 400 years later, many supply chain managers still struggle with the application of the premise. Different companies will have different criteria for measuring performance. For example, a pharmaceutical client would be much more concerned about batch controls and error rates than an appliance manufacturer would. But four basic rules should apply over all industries and providers.
First, is the tried and true, You can’t manage what you can’t measure. This is particularly valid for outsourced operations. If you do not know how the provider is performing against agreed-upon standards and benchmarks, it will be impossible to evaluate not only its performance, but the client’s own customer service.
Second, Make measurable what cannot be measured. The task here will be to identify activities in discrete segments against which you can establish measurable and achievable standards. A common mistake is to establish standards that are so vague they are absolutely meaningless. This creates additional work for both parties. Once the activities have been identified, then their performance can be determined.
Third, Measure only what is important and actionable. This is the area where a lot of big data is generated. It also often leads to “report abuse”. Some managers will become so fascinated with the reports themselves that they will insist on managing trivia. If it doesn’t have an impact on the operation or the operation’s cost, efficiency, or customer service, forget it. While very company has its unique needs, in a typical warehouse operation for example, the measurement of 8 to 10 basic areas should be sufficient. Examples of these are, productivity, order-fill rate, on-time performance, inventory variations, order cycle time, line-item accuracy, number of orders handled, and space utilization. You really don’t need to know how many orders were loaded at Door 5 by employees wearing blue shirts, and hauled away in red trucks.
Fourth, Measurement must be balanced. Too many measurements can bury the operation in details and lead to friction between the parties. Too few or too general evaluations will make the performance difficult to manage. Timing should be balanced, as well. There is no need to manage everything every day.
Certainly, as our technology continues to improve, we will learn more about our supply chains, i.e., generate more and bigger data and some of the information no doubt will be helpful. The phrase, “Information is Power.” probably has been quoted on millions of occasions, but in my opinion, the real power lies in being able to take the information and use it effectively. This includes rejecting the information you don’t need to manage your activities.